When it comes to understanding the inner workings of an air compressor, the Air Compressor Pressure Switch Wiring Diagram is a crucial component. This diagram provides a visual representation of how the pressure switch is wired within the compressor system, allowing individuals to troubleshoot and make necessary repairs. Understanding how to read and interpret this diagram is essential for anyone working with air compressors.
Why Air Compressor Pressure Switch Wiring Diagrams are essential
1. Provides a visual representation of the wiring connections within the air compressor system.
2. Helps in troubleshooting electrical issues related to the pressure switch.
3. Ensures that the pressure switch is correctly wired for optimal performance.
4. Allows for easy identification of components and their connections.
How to read and interpret Air Compressor Pressure Switch Wiring Diagram
1. Start by identifying the key components on the diagram such as the pressure switch, motor, power supply, and connections.
2. Follow the lines connecting the components to understand how they are wired together.
3. Pay attention to the symbols and labels used in the diagram to determine the function of each component.
4. Refer to the legend or key provided with the diagram for additional information on specific symbols or colors used.
Using Air Compressor Pressure Switch Wiring Diagram for troubleshooting electrical problems
1. Identify any loose or disconnected wires on the diagram that may be causing the issue.
2. Check for any damaged components such as switches or connectors that may need to be replaced.
3. Compare the diagram to the actual wiring in the air compressor system to see if there are any discrepancies.
4. Use a multimeter to test the continuity of the wires and connections to pinpoint the source of the problem.
Importance of safety when working with electrical systems
1. Always disconnect the power supply before working on any electrical components.
2. Wear appropriate personal protective equipment such as gloves and safety goggles.
3. Follow proper lockout/tagout procedures to prevent accidental startup of the compressor.
4. Avoid working on electrical components in wet or damp conditions.
5. If in doubt, consult a professional electrician or technician for assistance.
Air Compressor Pressure Switch Wiring Diagram
3phase Air Compressor Wire Connection | how to wire 3 phase air

Pressure Switch Wiring Diagram Air Compressor
how to install an air pressure switch in 3 ph motor – Irish Connections
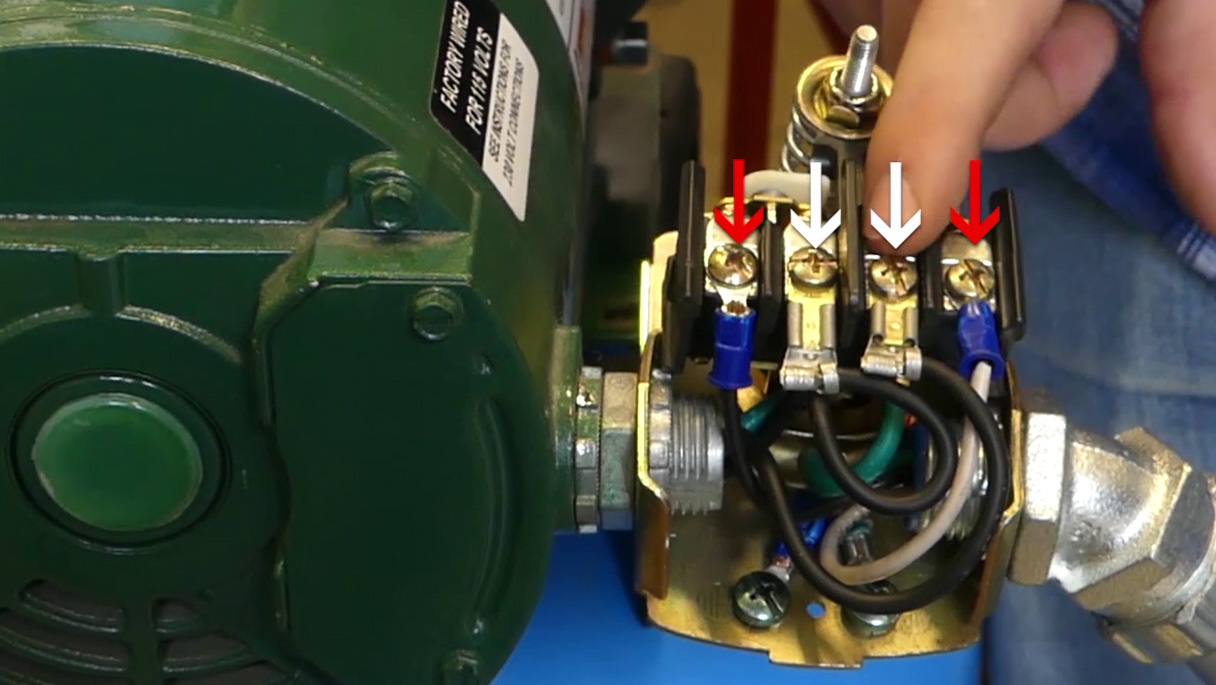
Wiring A Pressure Switch For Air Compressor

Air Compressor Pressure Switch Wiring

Air Compressor Pressure Switch Wiring diagram | Air Compressor
